The Role of Polished Aluminum Circles in Industrial Applications
In industrial production, materials that are durable, versatile, and cost-effective are essential. Among such materials that have emerged as a success in various industries is the polished aluminum circle. Being of shiny finish, high reflectivity, and excellent formability, the component is of crucial use in decorative and functional applications. From aluminum circle production to lighting and automotive use, the aluminum circle is still one of the top choices among engineers and manufacturers today.
What is Polished Aluminum Circle?
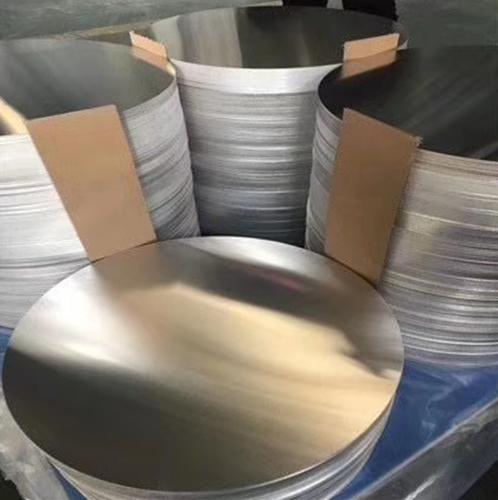
A polished aluminum disc is a high-purity aluminum, smooth, rounded disc that has been shaped to create a shiny, reflective surface. They are typically made from aluminum alloys such as 1050, 1060, 1100, or 3003, which offer high corrosion resistance, conductivity, and ductility. “Polished” refers to the surface treatment,t which contributes to the material’s beauty and brilliance. This last step can consist of mechanical polishing, chemical polishing, or a combination of both to obtain a mirror-finish surface that is bright, smooth, and uniform.
Polished aluminum discs are available in a variety of diameters and thicknesses, making them extremely versatile in a wide range of industrial applications. In addition to adding aesthetic appeal to the finished product, the polished surface also contributes to product functionality, particularly in applications where reflecting light, cleanliness, or ease of cleaning is important.
These circles have wide use in industries such as cookware, lighting, automobiles, electronics, and sign making due to their spinnability and performance. The fact that they can be deep drawn or spun into complex shapes without cracking makes them especially suitable for making products such as frying pans, reflectors, and decorative trims.
How Polished Aluminum Circles are Made?
The production of mirror-finish aluminum circles is a series of customized operations designed to provide precision, consistency, and excellent surface quality.
- This begins with the use of high-quality aluminum coils, chosen for purity and formability. These coils are first cleaned and pre-treated to remove surface contamination or oxidation that could interfere with the final polish.
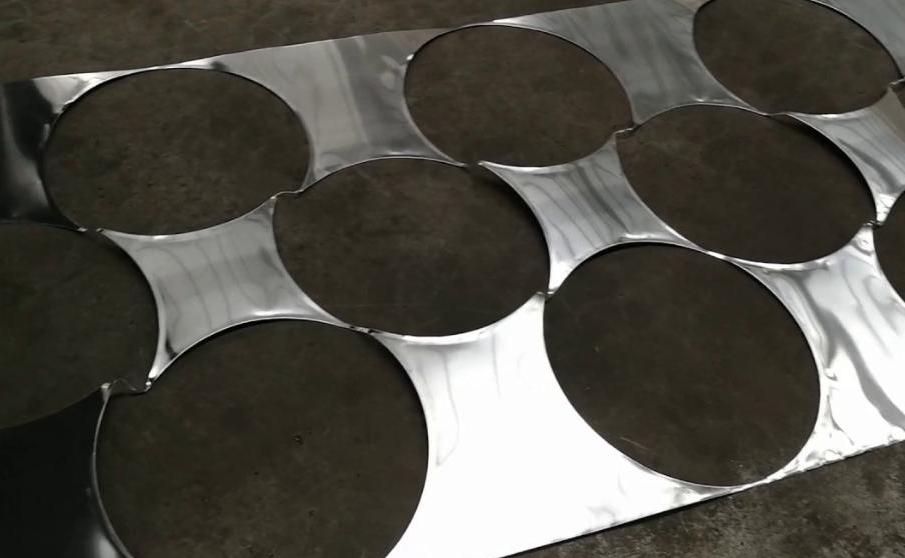
- The aluminum is then run through precision circle-cutting machinery, which punches out discs with very exact diameters and thicknesses. Blanking is stringently controlled to maintain close tolerances, ensuring consistency in large order runs.
- Once the raw circles are established, they undergo a surface enhancement. Unlike unfinished aluminum discs, polished aluminum circles require additional surface conditioning through multi-stage polishing techniques. These can include mechanical buffing with fine abrasives, chemical treatments for enhanced brightness, and even protective coatings to sustain the finish.
Temperature, handling, and surface pressure are all carefully regulated in the process to prevent scratching or warping. The result is a flawless, reflective disc ready for demanding industrial applications. Each batch is inspected not only for dimensional accuracy but for gloss level and surface clarity as well.
Key Benefits of Polished Aluminum Circles in Industry
The shiny finish of aluminum discs is more than just physically appealing—it is the essential factor for enhanced performance during industrial use.
- Among the most important benefits is superior reflectivity, which makes the discs best for applications that require efficient light dispersal, like LED lighting equipment and solar reflectors.
- In addition to reflectivity, the reflective, mirror-like surface of polished aluminum increases cleanliness and hygiene, especially important in cookware and medical device manufacturing. The polished surface resists stains and is easier to sanitize, conserving maintenance time and delivering product safety.
- Furthermore, polishing enhances corrosion resistance in aluminum by creating a more uniform and sealed surface, reducing opportunities for oxidation and surface degradation. The final product has an extended lifespan and even appearance in adverse conditions.
- Polishing also enables enhanced formability, with smoother surfaces reducing friction during spinning and deep drawing processes, thus fewer defects during shaping.
In total, the smooth finish dramatically enhances both the usability and toughness of aluminum discs in the industrial setting.
Industrial Applications of Polished Aluminum Circles
Polished aluminum discs have widespread uses in industries due to their excellent surface finish, durability, and functional properties. Four of the most important uses are explained below in detail:
1. Cookware & Kitchenware Manufacturing
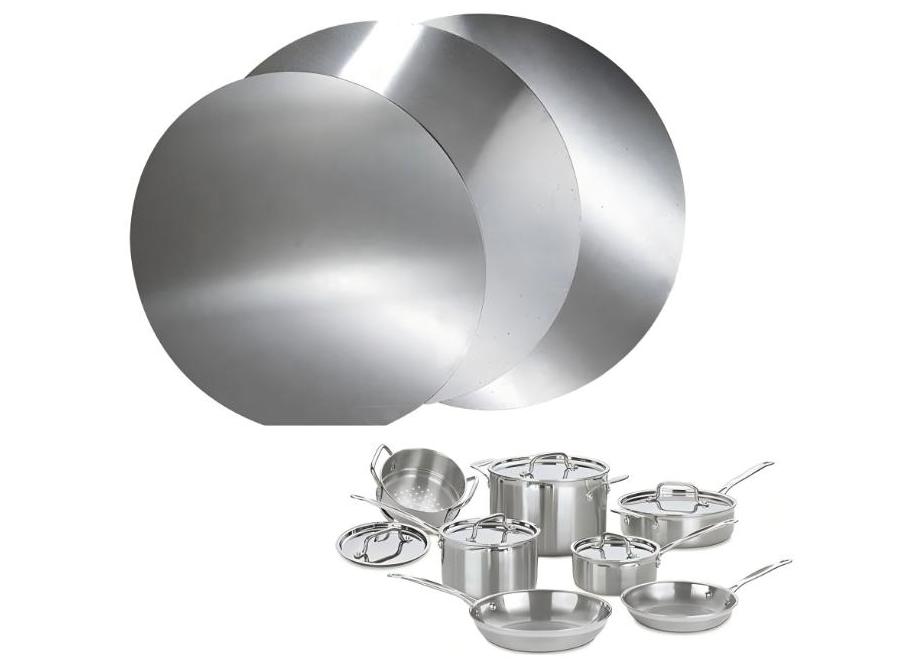
Polished aluminum discs are a popular choice for making high-quality cookware, including pots, pans, covers, and baking sheets. The reflective, smooth finish enhances non-stick characteristics when coated, enabling even heat conductivity and easy release of food. The polished surface is also corrosion-resistant to acidic foods, which enhances the longevity of kitchen utensils. The clean and easy-to-clean surface further meets food safety standards, qualifying it for use in commercial and household cookware.
2. Lighting & Reflectors (LED, Automotive, Solar)
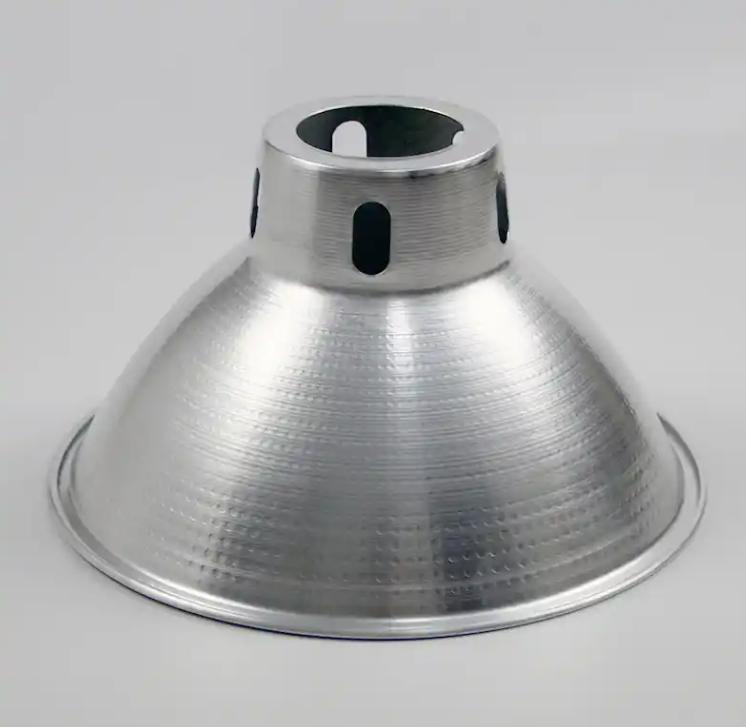
Polished aluminum discs are perfect for lighting applications because of their high reflectivity. In LED luminaires, they enable maximum light output by reflecting and guiding light efficiently. In headlight units for the automotive sector, polished aluminum reflectors deliver higher brightness and beam precision. In solar energy systems, the discs are used in concentrated solar power (CSP) reflectors for sunlight concentration onto receivers to increase energy conversion efficiency. The polished surface minimizes excessive scattering of light, which optimizes its use in optical applications.
3. Decorative & Architectural Features
Polished aluminum discs have widespread uses in signage, trophies, decorative panels, and interior design due to their luxurious, mirror-like appearance. Their resistance to tarnishing offers long-lasting luster, which makes them ideal for high-end retail displays, awards, and architectural cladding. The lightness of aluminum, coupled with its strength, facilitates easy installation in facades, ceilings, and artistic installations, where aesthetics are combined with structural strength.
4. Automotive & Aerospace Parts
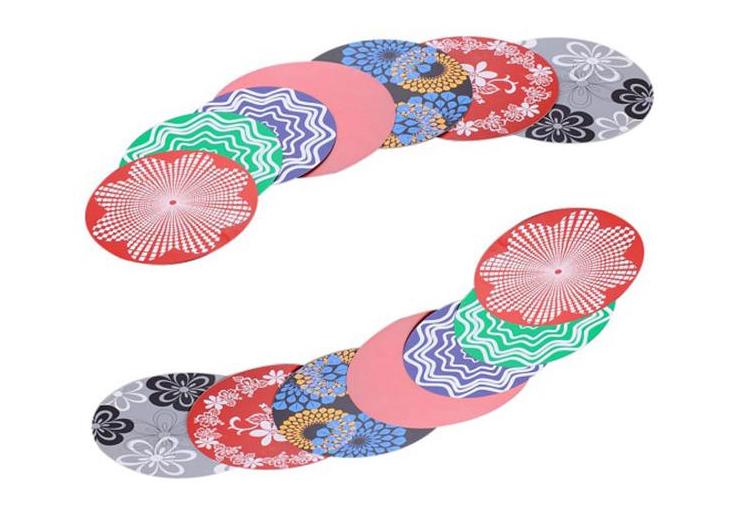
In the automotive industry, they use polished aluminum discs for trim, emblems, wheel covers, and heat shields, where both function and looks matter. The polished finish resists environmental wear and tear while appearing high-quality. In aerospace, they are used in reflectors, satellite components, and thermal management systems, where weight reduction and corrosion resistance are crucial. The smooth surface also helps in reducing air friction in some aerodynamic uses.
Do You Need Bulk Polished Aluminum Circles?
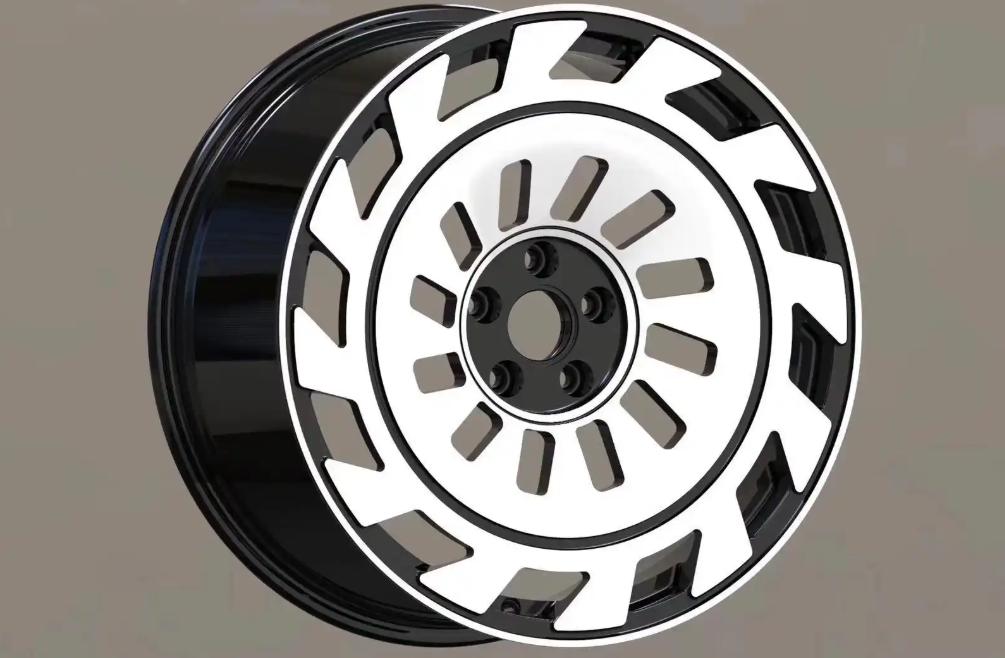
If your business requires high-quality, bulk polished aluminum circles, choosing a veteran and professional manufacturer can ensure consistent performance, precision, and timely delivery.
Lanren is a top polished aluminum circle manufacturer in the industry. Lanren has decades of experience and is professional in producing aluminum circles with good surface finish, stable thickness, and fine formability. Their modern production lines and strict quality control ensure that every batch is of an international standard for industrial and consumer applications. We offer a wide range of alloys, sizes, and finishes to meet the specific requirements of customers in various industries. Their ability to supply customized solutions in bulk has made them a supplier of choice for brands worldwide.
If you’re looking for a trusted bulk polished aluminum circles supplier, Lanren combines technical expertise, manufacturing capability, and considerate customer service to support your business every step of the way.
Related Products