Aluminium Circle Surface Treatments for Corrosion Resistance in Lighting Applications
Aluminum circles are frequently used in the lighting industry to produce luminaries, reflector surfaces, or housings for LED panels. They are frequently employed in areas of extreme temperatures, humidity as well as other environmental conditions. Therefore, resistance to corrosion is vital to ensure the highest standard of product as well as its longevity. Applying the correct treatments for aluminum circles do more than increase its resistance to corrosion. They also enhance the appearance of the surface and increase its endurance, especially for circle aluminum light that demand both durability and functionality.
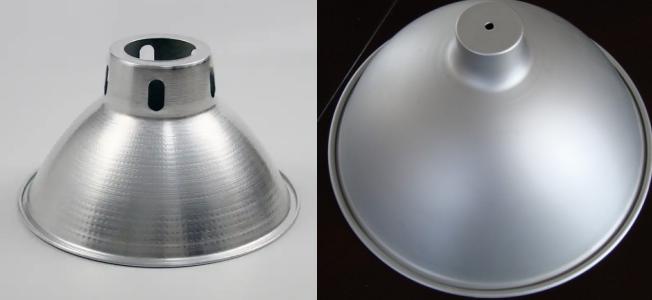
Corrosion Resistance Matters for Lighting Aluminium Circles
Lighting products, particularly made specifically for outdoor, industrial or humid environments are susceptible to rust due to constant exposure to the elements of air, humidity, pollution as well as ultraviolet light. Damaged parts of aluminium could cause their the strength of the material to decrease as well as affect aesthetics with discoloration, and reduce the performance of light reflection, and reduce the lifespan of products.
To tackle these issues To address these issue, aluminum circles that are used in lighting fixtures require treatment that increase their resistance to oxidation, moisture as well as environmental damage.
Common Surface Treatments for Lighting Aluminium Circles
To enhance resistance to corrosion and obtain a high-quality surface, various surface treatments are applied on aluminum circles in the course of the process of production process:
1. Anodizing
Anodizing is the most well-known method of lighting aluminum circles.The electrochemical process creates an even and dense oxide layer on the aluminum surface. The anodized layer dramatically increases wear resistance and the surface’s hardness. It also provides excellent colour stability. This is crucial in lighting equipment that need an even, clean appearance in time.
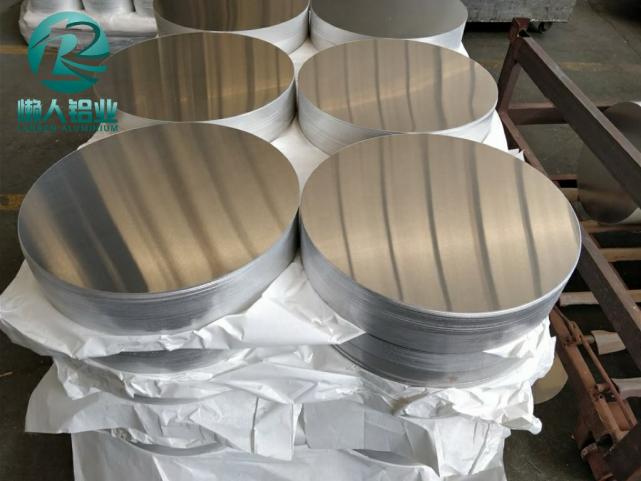
2. Sandblasting
Sandblasting is typically used prior to the coating or anodizing process for circle aluminum light parts. It removes dirt from the surface of aluminium, removes impurities, and produces a smooth surface that increases the adhesion of any subsequent treatment. For lighting applications, it increases the longevity of the coating and also ensures an even surface.
3. Polishing
Polishing improves the brightness and reflectivity of aluminum circles. This is essential for lighting reflectors, a key component in circle aluminum light designs. The process of polishing also increases surface smoothness, which minimizes potential corrosion initiation points, and improves general appearance and look of the lighting components.
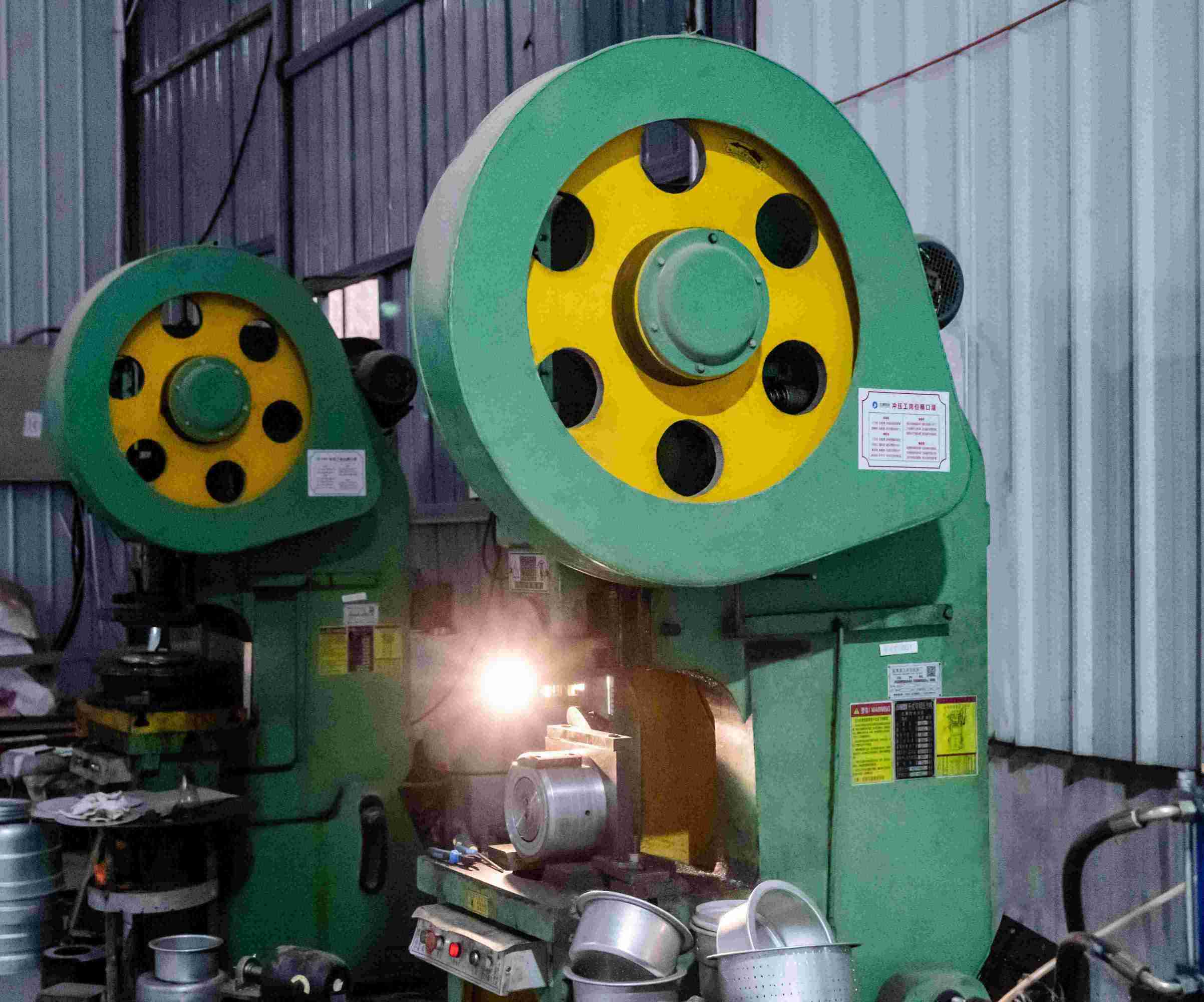
Beyond the raw materials, expense of transforming aluminum ingots into finished circular shapes is a major factor in the expense. This involves cold and hot rolling and cutting, annealing, stamping, as well as other procedures. The degree of complexity in the manufacturing process is determined by the specifications required. For example, circular shapes which require a smooth surface as well as tight tolerances or specific mechanical characteristics are subject to more intense process, which will increase expenses. In addition, the cost of labor along with equipment maintenance and energy usage add to the total cost of processing, particularly those in areas that have significant labor or utility costs.
4. Coating
Other protective coatings, such as clear lacquers, or color coatings, can be obtained by polishing, or even anodizing. These coatings provide protection against moisture and chemicals and can further increase the resistance to corrosion, as well as providing decorative effects to lighting fixtures of top quality-an important feature for circle aluminum light products that need to balance functionality with visual appeal.
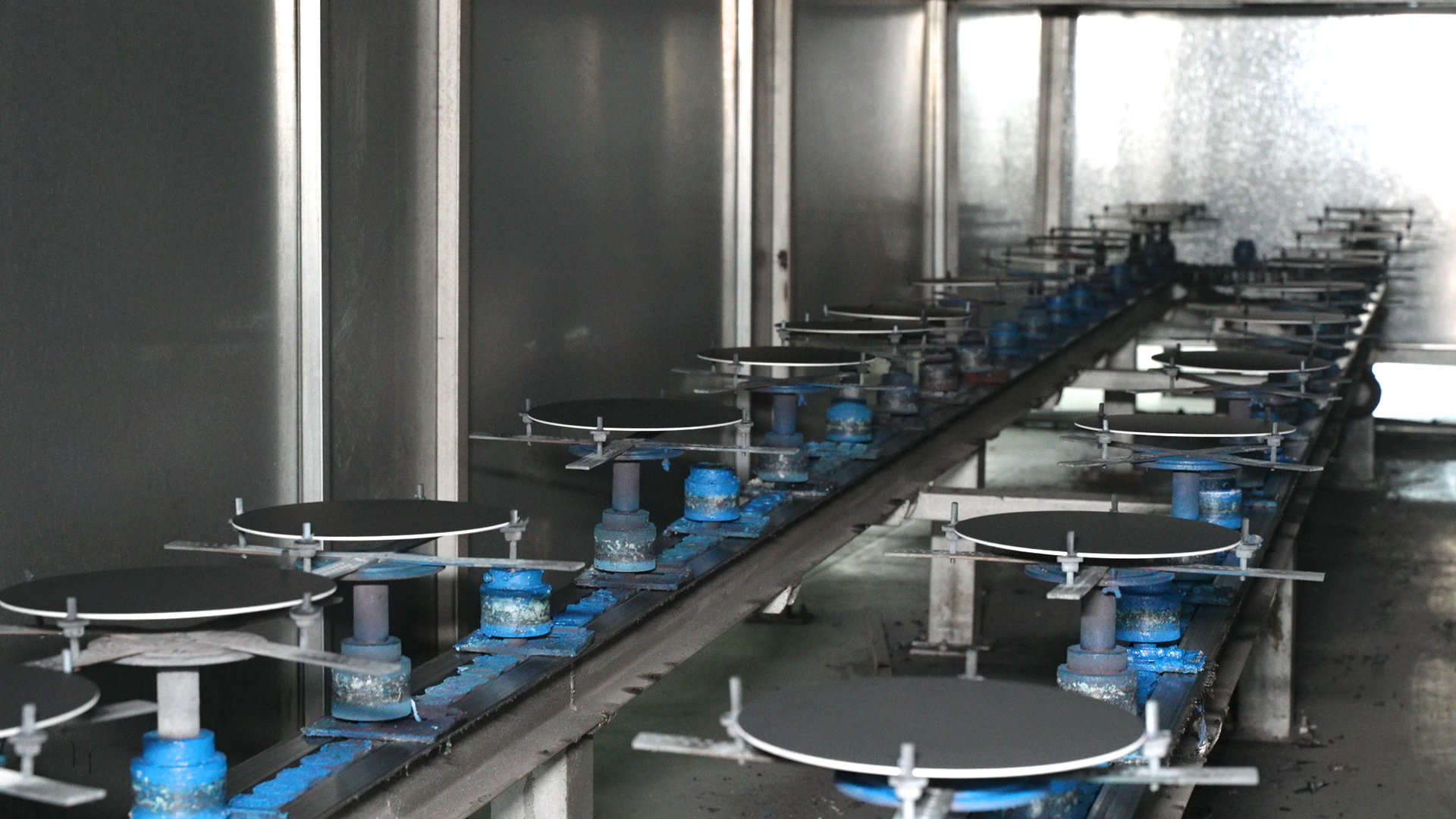
Surface Treatment | Key Function | Advantages in Lighting Applications |
Anodizing | Enhances wear resistance, hardness, and color stability | Maintains a clean appearance over time; ideal for outdoor/industrial environments requiring corrosion resistance |
Sandblasting | Improves adhesion of subsequent treatments | Increases durability of coatings/anodizing; ensures surface uniformity |
Polishing | Reduces corrosion initiation points; boosts light reflection | Optimizes lighting efficiency; enhances brightness and range of luminaries |
Coating | Resists moisture and chemicals; adds decorative value | Further improves corrosion resistance; offers diverse colors |
The advantages of surface treated aluminum Circles for Lighting
Superior Corrosion Resistance
The aluminum circles that are coated with oxide or a coating that resists moisture, oxidation, and as exposure to UV. This extends the life of the product, even in harsh environments. Other coatings that provide protection, such as clear lacquers or color coatings, are offered by polishing and even anodizing. These coatings protect against chemical and moisture, and improve their resistance against corrosion, and also provide a decorative effect to light fixtures from the finest materials.
Enhanced Reflectivity
The polished or anodized aluminum circles have reflective surfaces that increase the efficiency of lighting and enhances its performance. In lighting fixtures that require reflectivity for reflection, like the case of car headlights or stadium floodlights. The use of aluminum circles treated with a surface can dramatically improve the power and range of lighting, and provide better visibility.
Aesthetic Appeal
The aluminum circles treated with treatment have elegant and uniform surfaces. They come in different colors and finishes that match lighting styles, and also incorporate decorative elements. It’s a sleek and modern design for contemporary lighting or a traditional, polished finish for classic designs, aluminum circles treated with surface treatment will satisfy a range of aesthetic needs.
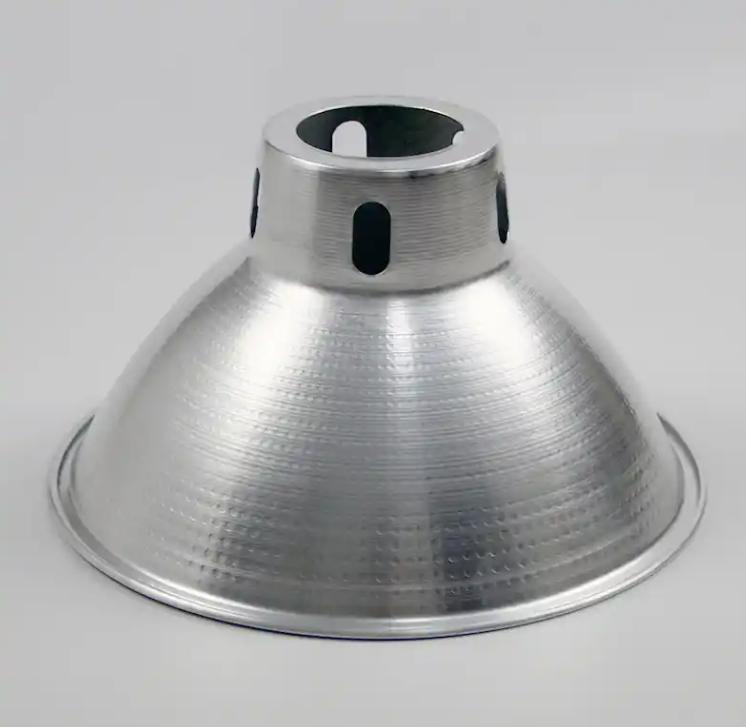
Better longevity
The surface treatments of aluminum circles enhance resistance to wear and scratches making sure that lighting components remain sleek and sturdy for a long time. This does not just reduce the requirement for regular replacements, but also improves the long-term sustainability of products that are made from processed aluminum circle-a cost-effective advantage for manufacturers and users of circle aluminum light systems.
Lanren Aluminium for Lighting Aluminium Circles
At Lanren Aluminium, we specialize in the production of premium aluminum circles specifically designed for lightweight as well as other uses. Our products are built from the finest aluminum alloys like 1050, 1060, 1100, 1070, along with the 3003 series. These alloys provide outstanding resistance to rust and outstanding working capabilities, making them ideal for circle aluminum light applications. Lanren is a trusted Lighting Aluminum Circle Manufacturer in China, equipped with modern polishing and anodizing facilities, modern manufacturing lines that assure homogeneous surface.
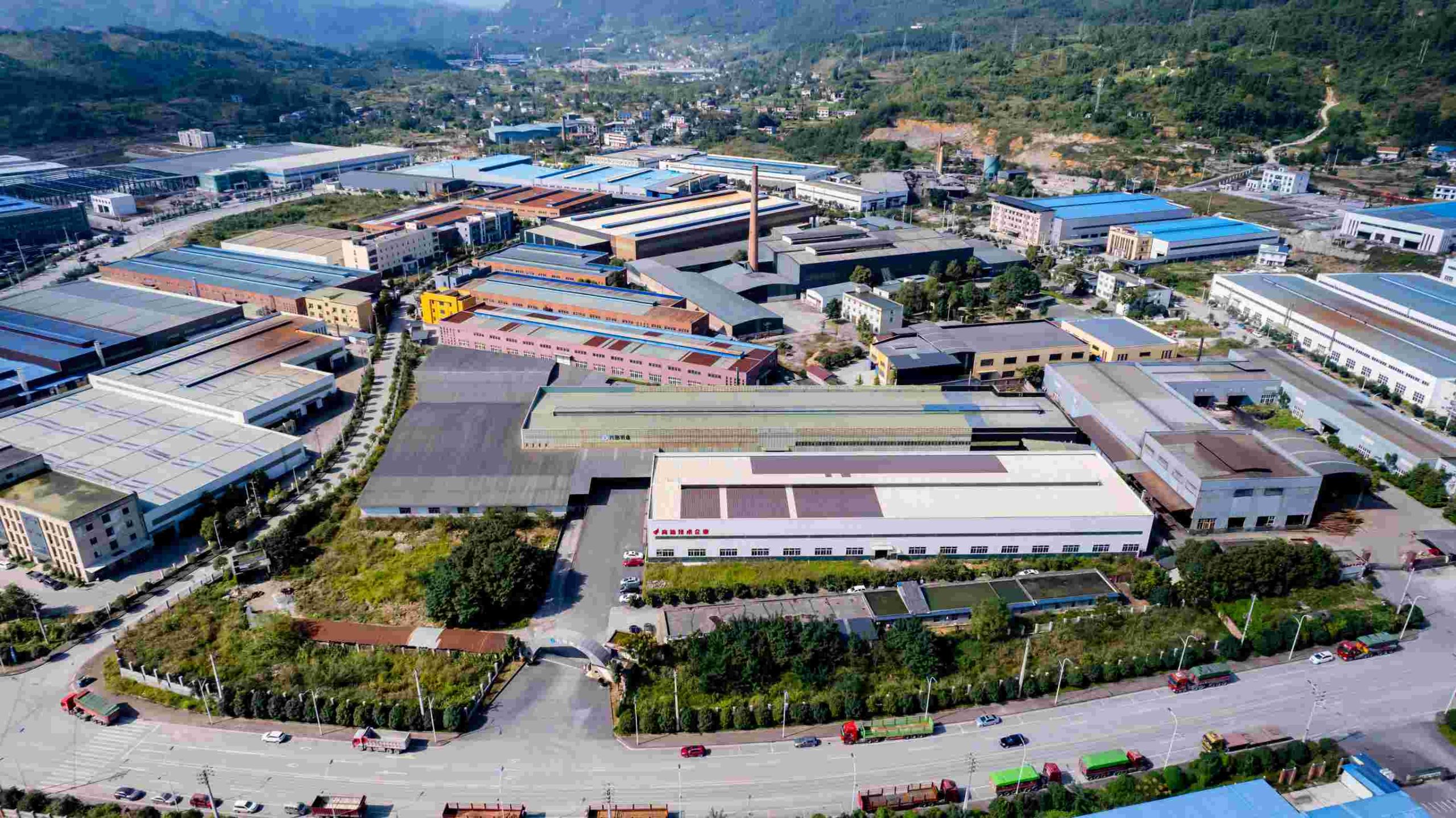
It is essential for aluminum circles employed in lighting applications because it directly affects the life of the product in addition to aesthetics and safety. Polishing anodizing, sandblasting, and polishing coatings that protect significantly improve the endurance and performance of aluminum lighting circles. Lanren Aluminium offers high-quality, solid aluminum circles designed by professional surface treatment experts. This allows lighting firms to design products that are built to endure the most demanding conditions.
Contact us today to find out how we can help you with lighting solutions and custom-designed procedures services.consistent fine oxide which exhibits an exceptional amount of reflection.
Related Products