How to Reduce Material Waste When Cutting Aluminum Sheets
Aluminium is one of the most adaptable materials, used across numerous industries from automobile production and design to construction and manufacturing. Unfortunately, cutting aluminum sheets often results in material waste, which both harms the environment and drives up production costs; however, there are effective strategies and tools that can reduce this waste, creating a more efficient and eco-friendly cutting process.
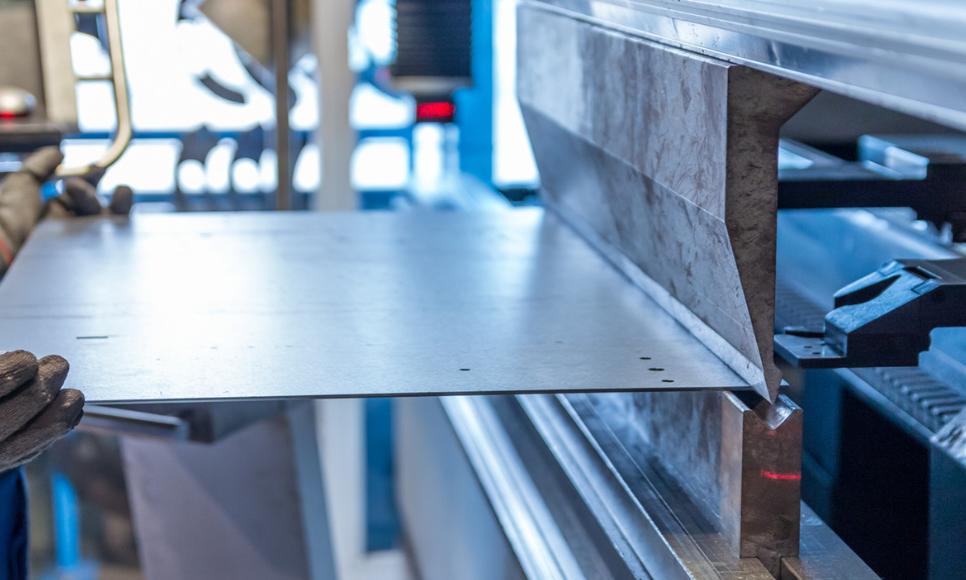
Why Reducing Waste in Aluminum Cutting Matters
Metal fabrication represents both lost profits and inefficiency; with material costs continuing to climb and sustainability taking priority, minimizing waste during cutting operations can provide three key advantages. These are:
- Cost Savings: Aluminum sheet waste has an immediate and direct effect on your bottom line, and even a 5- 10% decrease can add up to significant annual savings, especially among high-volume manufacturers.
- Environmental Advantages: Aluminum may be recyclable, yet production remains energy-intensive. Reducing waste means decreased energy usage and carbon emissions–an essential consideration for environmentally aware industries.
- Operational Efficiency: Wasted material leads to additional orders, delays in timelines, and extra labor expenses. With precision cutting techniques, ensuring smooth production flow and increasing raw material usage.
Industries such as automotive, aerospace, and construction prioritize waste reduction to meet strict budget and sustainability targets. By optimizing cutting processes or using custom-cut aluminum sheets for custom cuts, businesses gain a competitive edge while cutting unnecessary costs.
Best Tools for Cutting Aluminum Sheets with Minimal Waste
If you want to cut aluminum efficiently, in addition to choosing high-quality aluminum sheets that meets your needs, you also need the right tools to maximize material utilization and reduce waste. The following are the most efficient cutting methods that balance accuracy, speed and reduced waste:
- Laser Cutting for Precision and Thin to Medium Sheets
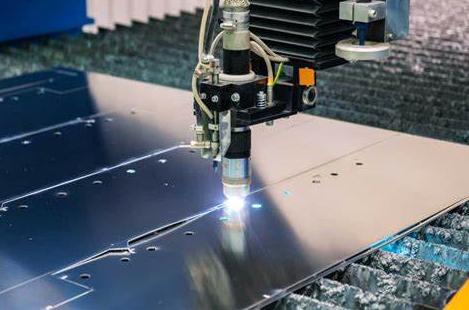
Laser cutting provides exceptional accuracy, making it an excellent solution for intricate designs that have tight tolerances. With its narrow kerf width of only 0.1-0.3mm and waste material waste rates between 0.1% and 0.3% compared with traditional sawing processes. It works best on thin to medium aluminum sheets (0.5-25mm thickness). Typical applications for this method of production are electronics manufacturing and automotive assembly plants.
Key Benefit: Minimized material loss due to high precision.
2. Water Jet Cutting for Thick Sheets without Heat Distortion
Unlike laser or plasma cutting, water jet technology uses a high-pressure stream of water mixed with abrasives to cut aluminum without creating heat distortion, thus preserving material integrity without warping. Specifically designed to work on thick sheets up to 150mm in thickness and widely utilized by aerospace and marine applications.
Key Benefit: No heat-affected zones mean less material wasted from warping, saving both money and resources in terms of material waste.
- CNC Routing – For Automated, Repeatable Cuts
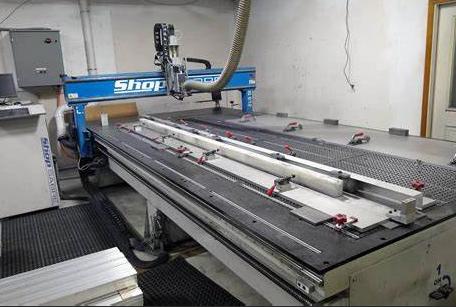
CNC routers equipped with high-speed spindles and carbide bits provide consistent, repeatable cuts—ideal for bulk orders. Advanced nesting software optimizes sheet layouts, reducing scrap by up to 20% compared to manual cutting. This method is popular in signage, cabinetry, and industrial fabrication.
Key Benefit: Software-driven efficiency maximizes sheet utilization.
4. Shear Cutting vs. Circular Saws – For Simple, Straight Cuts
Shearing is fast and efficient for straight cuts but limited to basic shapes.
Circular saws with fine-tooth carbide blades are cost-effective for workshops but require proper technique to avoid jagged edges and excess waste.
Best for: Small shops needing quick cuts without high-tech equipment.
Choosing the Right Tool = Less Waste, Lower Costs
Each method has trade-offs between speed, precision, and cost. For zero-waste cutting, many manufacturers now opt for pre-cut aluminum sheets from suppliers, eliminating in-house scrap entirely.
Techniques to Minimize Cutting Aluminum Sheets Waste
Reducing waste when cutting aluminum sheets starts with smart planning and efficient cutting practices. One of the most effective methods is nesting optimization—the strategic arrangement of parts on a sheet to use as much material as possible. Nesting software can automatically position parts tightly together, minimizing gaps and leftover scrap. This technique ensures that more components can be produced from a single sheet, maximizing yield.
- Selecting the ideal tools is equally essential to producing quality aluminum parts. Use saw blades, cutters, and machines designed specifically to cut aluminum with suitable material thickness in mind; using fine-tooth blades on thin sheets reduces material loss at the cut and minimizes edge damage that could otherwise lead to rejected parts.
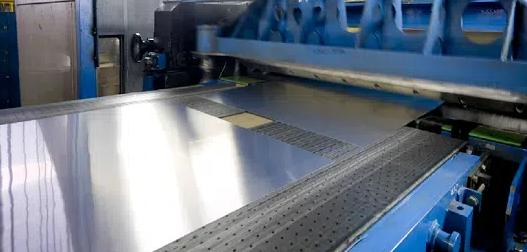
- Pre-cut planning plays a pivotal role in aluminum fabrication projects. Before cutting anything out, assess how offcuts could be reused for other smaller components or future projects; even small sections can prove valuable if planned carefully. Designing parts with standard sizes or compatible dimensions makes repurposing off-cuts much simpler.
- Proper machine calibration – including accurate speed, pressure, and feed rates – is paramount. Cutting too quickly may create burrs or warping while too slowly may waste time or produce uneven results; maintaining and calibrating machines ensure clean cuts with minimum errors and waste.
- Lastly, accurate measurements and layout markings help avoid mistakes that result in wasted sheets. Double-check dimensions before cutting and use precise marking tools to ensure alignment. When cuts are made correctly the first time, material use is optimized and scrap is reduced.
By combining strategic planning, the right equipment, and disciplined execution, manufacturers can significantly reduce aluminum sheet waste and improve overall production efficiency.
Benefits of Custom Cut Aluminum Sheet Services
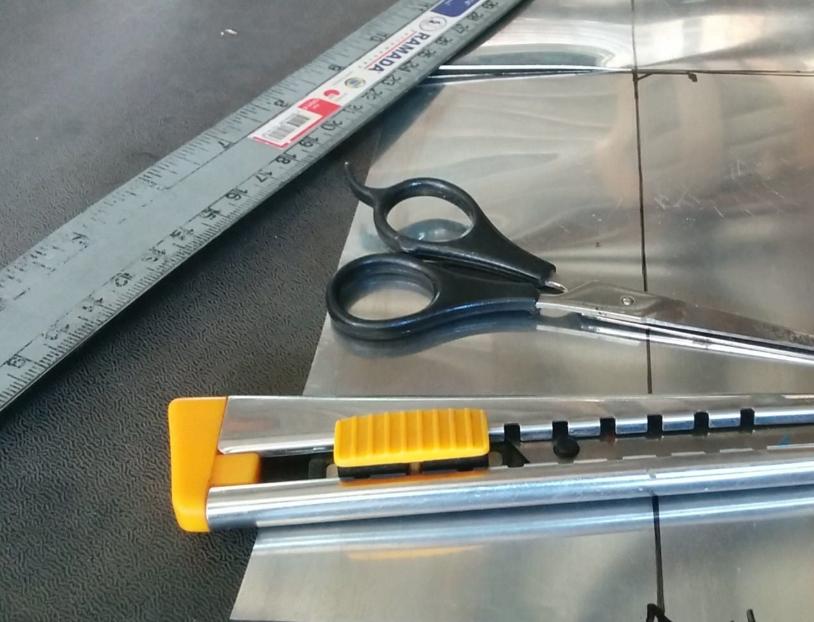
Choosing custom-cut aluminum sheet services can bring many advantages that can streamline operations and reduce material waste, including:
- Precision Cutting Services: Custom cutting services employ cutting tools like CNC machines, laser cutters, and water jets for highly precise cuts that reduce measurement errors while meeting the exact specifications of parts to minimize material losses and waste.
- Reduce Waste: Professional services frequently utilize nesting software to maximize material utilization. By carefully planning cuts, they reduce scrap and make fuller use of each aluminum sheet available for sale.
- Time Efficiency: Custom cut providers specialize in handling large or complex orders quickly and precisely, expediting production timelines while cutting downtime associated with cutting in-house.
- Expertise and Quality Control: Aluminum cutting services provided here are managed by specialists with years of experience, who guarantee consistency and quality throughout every piece produced. Their processes have been optimized to produce consistently excellent results that deliver repeatable, repeatable high-grade results every time.
Utilizing custom cutting services is an efficient and cost-cutting strategy for manufacturers looking to increase efficiency and material utilization.
Reducing material waste when cutting aluminum sheets is key for improving sustainability, cutting costs and increasing efficiency. By choosing appropriate tools and employing effective techniques such as custom cut services, businesses can realize significant material and time savings, all while decreasing environmental impacts. From CNC cutters to expert services specializing in aluminium waste reduction reducing aluminum waste is one step towards more eco-friendly production lines.
Related Products