Mill Finish Aluminium Circle vs. Anodized Aluminium Circle for Industrial Applications
Aluminum circles are an excellent material choice for industrial applications due to their lightweight, corrosion resistance, and thermal conductivity properties. When choosing between mill finish aluminium circles and anodized aluminium circles for specific use cases, however, mill finish and anodized varieties may significantly impact performance and lifespan – this guide explains the differences between them in order to help you determine which option is most suitable.
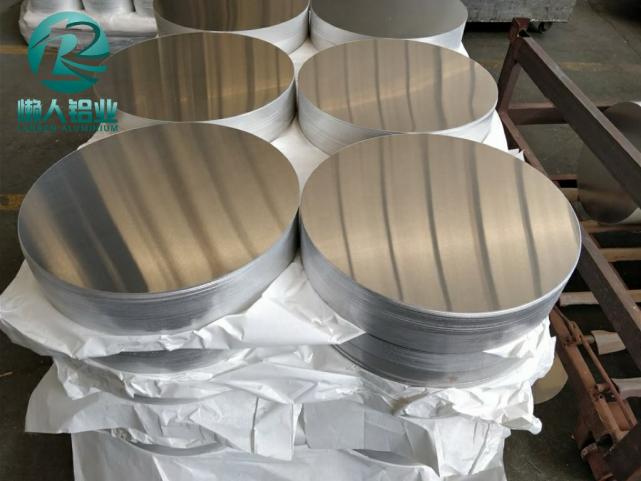
What is Mill Finish Aluminium Circle
The mill finish Aluminum circles are raw, uncoated aluminum discs that have retained their natural surface straight from the rolling machine. Unlike polished or anodised aluminum, they do not go through any additional finishing processes, giving them a slightly rough, matte appearance with a metallic sheen.
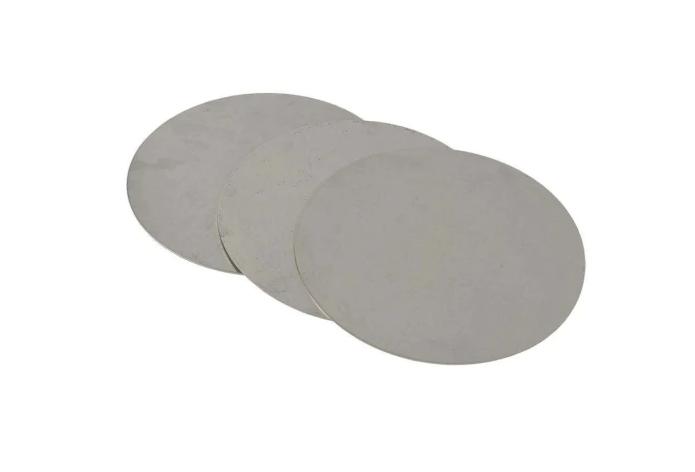
These circles are valued for their low cost and adaptability, making them perfect for applications where practicality takes precedence above surface aesthetics. Because they are not treated, they can be easily cut, stamped, spun, or machined into a variety of shapes, including cookware, reflectors, and industrial components.
However, mill finish aluminium is more prone to oxidation and scratches than treated aluminium. Some manufacturers use protective coatings or additional processing techniques such as polishing or painting to ensure long-term durability.
The Key Advantages:
- Lower production cost (no extra finishing steps)
- Excellent formability for fabrication
- Suitable for secondary processing (painting, coating, etc.)
Common uses include kitware, lighting components, and general industrial parts where a refined surface finish is not critical.
What is Anodized Aluminium Circle
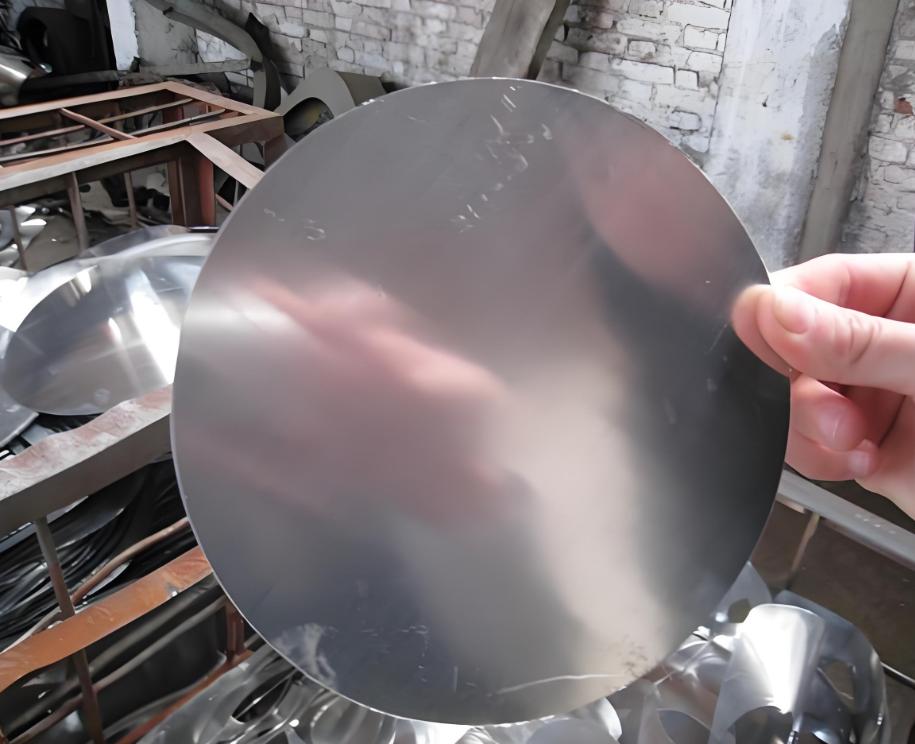
Anodized aluminum circles go through an electrochemical procedure that strengthens their natural oxide layer, resulting in a long-lasting and corrosion-resistant surface. This anodizing process involves immersing aluminum in an acid electrolyte bath and applying an electric current to build the oxide layer and seal the pores. As a result, the material becomes stronger, more wear-resistant, and can be dyed in a variety of colors for aesthetic purposes.
One of the primary advantages of anodized aluminum is its great resilience to environmental conditions, making it perfect for outdoor and high-wear applications. Unlike mill finish aluminum, anodized circles do not require extra coatings for protection because the process itself provides long-term protection against oxidation, UV rays, and chemical exposure.
Additionally, anodized aluminium offers better adhesion for paints and adhesives, making it suitable for industries requiring printed or bonded components. Common applications include architectural panels, automotive trim, electronic housings, and high-end consumer products where both durability and visual appeal are essential.
Comparison: Mill Finish vs. Anodized Aluminium Circles
When selecting aluminium circles for industrial purposes, it is critical to understand the key differences between mill finish and anodized variants. Mill finish aluminum provides a low-cost raw material solution with great formability, making it appropriate for applications requiring secondary processing. Its natural oxide layer provides basic corrosion protection, but long-term exposure to hostile environments may necessitate additional protective coatings. The unpolished surface is ideal for components where looks come second to functionality, such as spun cookware or reflector panels.
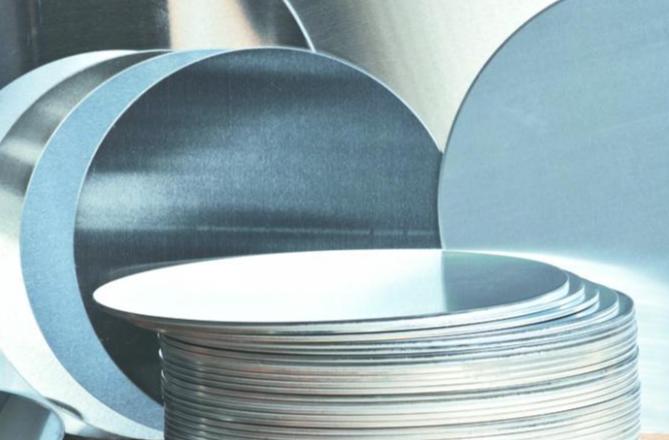
In contrast, anodized aluminium circles function well in harsh environments. The electrochemical anodizing technique produces a dense oxide layer, which improves corrosion resistance, surface hardness, and durability. This treatment also enables color customisation by dyeing, making it ideal for architectural and consumer-facing applications. While anodized aluminium is more expensive than mill finish, its endurance and lower maintenance requirements can outweigh the greater initial cost in crucial applications.
The choice between these two types ultimately depends on project requirements for durability, appearance, and budget. Below is a detailed comparison:
Property | Mill Finish Aluminium Circle | Anodized Aluminium Circle |
Surface Characteristics | Natural matte finish, slightly rough | Smooth, uniform, color options available |
Corrosion Resistance | Moderate (requires protection in harsh environments) | Excellent (built-in oxide barrier) |
Hardness & Durability | Standard aluminium hardness | Increased surface hardness (resists scratches) |
Cost Considerations | Lower initial cost | Higher due to processing, but lower lifetime costs |
Aesthetic Flexibility | Limited (requires post-processing for colors) | Wide color range, premium finishes |
Maintenance Requirements | Regular cleaning/protection needed | Low maintenance, easy to clean |
Common Applications | Cookware, reflectors, industrial blanks | Architectural cladding, automotive, electronics |
This comparison highlights how each type serves distinct industrial needs, with mill finish being the economical choice for fabrication projects and anodized excelling in high-performance, decorative applications.
Choosing the Right One for Different Industrial Applications
Selecting between mill finish and anodized aluminium circles depends on the specific demands of your industrial application. Below are key industry uses with detailed considerations for each type:
Cookware & Kitchenware Manufacturing
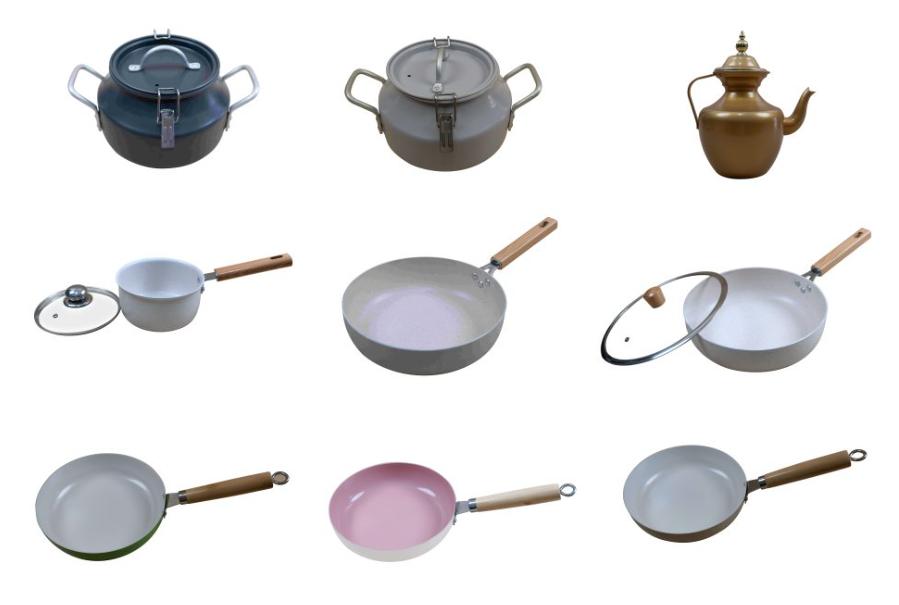
Mill Finish Aluminum Circles are the preferred material choice for pots, pans and pressure cooker bases due to their soft yet malleable nature allowing deep drawing without cracking, as well as being an excellent base material when polished or non-stick coated for use in cookware.
Anodized Aluminium Circles are used in premium cookware where scratch resistance and easy cleanup are key features. Hard-anodized cookware offers superior durability; however, its higher cost makes mass-produced items less common.
Lighting & Reflectors
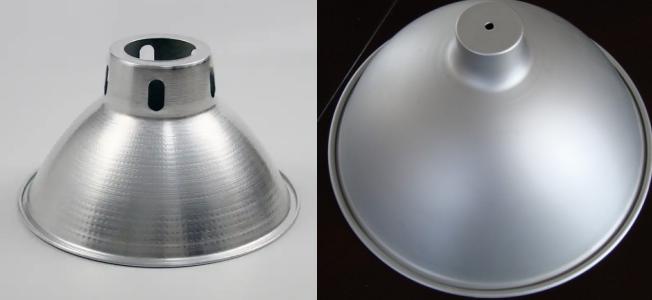
Mill Finish is ideal for reflectors and lamp housings because its natural bright surface offers excellent light reflectivity without additional treatment. The cost-efficiency makes it suitable for large-scale production.
Anodized Aluminium is used in high-end lighting fixtures where corrosion resistance (e.g., outdoor lighting) or colored finishes (decorative lighting) are required. The anodized layer prevents oxidation, maintaining reflectivity over time.
Automotive Components
Mill Finish is commonly used for interior structural parts, heat shields and brackets in which surface finish isn’t crucial. Due to its lightweight composition and formability, mill finish material makes an excellent choice for stamped or machined components.
Anodized aluminium is widely chosen for exterior trim, wheels, and decorative accents due to its weather resistance and aesthetic appeal. Furthermore, its hard anodized layer protects against road debris accumulation and chemical exposure.
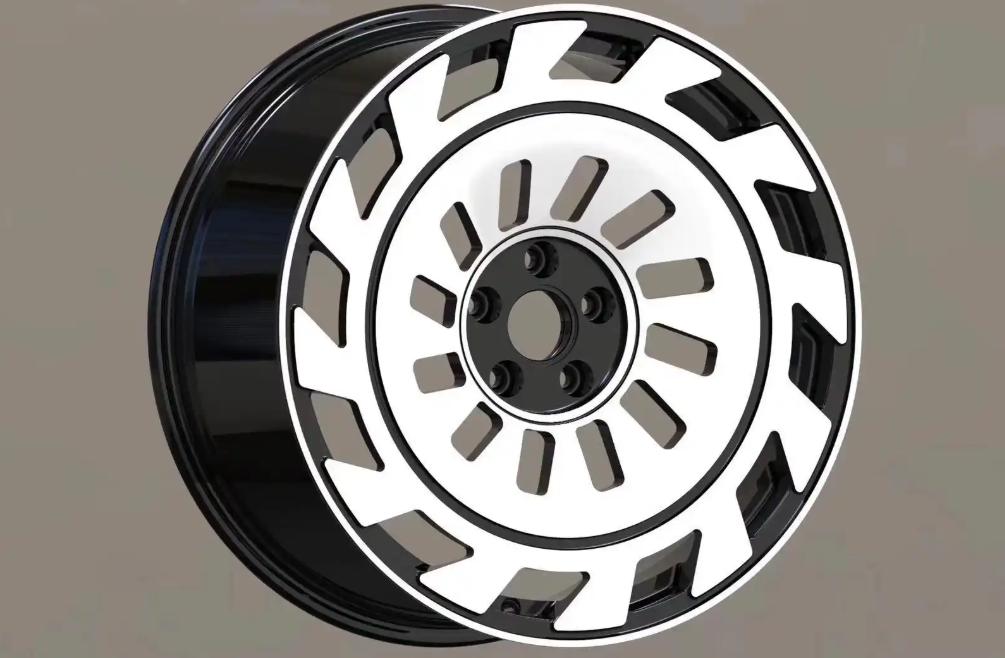
Architectural Cladding & Decorative Panels
Mill Finish is rarely used in architecture unless painted or powder-coated, as it lacks weather resistance. It may serve as a base material for further finishing.
Anodized Aluminium dominates in facades, signage, and interior design because of its color stability, UV resistance, and low maintenance. The anodized layer ensures decades of performance without fading or peeling.
Electronics & Heat Sinks
Mill Finish can be utilized on basic heat sinks and electronic enclosures where thermal conductivity is the priority and surface treatment is unnecessary.
Anodized aluminium is widely considered the premier material for high-performance heat sinks due to its anodized layer that improves heat dissipation while simultaneously protecting it against corrosion and thermal radiation. Black anodized finishes also enhance thermal radiation.
To Conclude
Decisions between mill finish and anodized aluminium circles depend on your project priorities. Mill finish provides cost savings and easy workability, which makes it suitable for applications where further processing will occur. Anodized aluminum offers superior durability, corrosion resistance, and aesthetic appeal, making it suitable for high-performance or decorative uses. By considering factors like environmental exposure, budget constraint, and surface requirements, manufacturers can select an appropriate material to maximize long-term performance and efficiency.
Related Products