What Makes 8000 Series Aluminum So Unique?
The 8000 series aluminum alloys (AA8000) are a category of wrought aluminum alloys primarily designed with non-traditional elements like iron (Fe) and silicon (Si). These alloys have carved a niche in industrial applications due to their unique composition, balanced properties, and cost-effectiveness. Compared to traditional aluminum alloys (e.g., 1000 series pure aluminum and 5000 Al-Mg alloys), the 8000 series aluminum strikes an optimal balance between electrical conductivity, mechanical strength, and workability, while maintaining advantages such as low density and high corrosion resistance. This article explores the distinctive value of 8000 series aluminum through its composition, performance, applications, and market competitiveness.
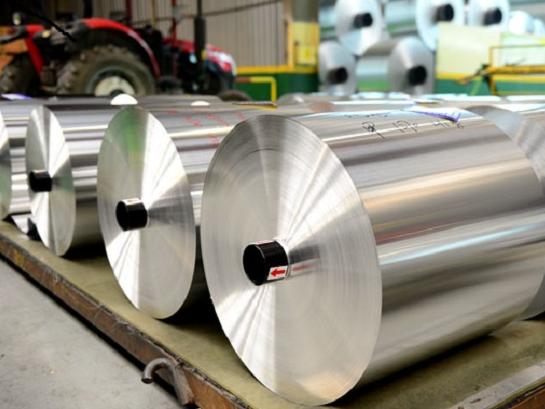
Alloy Composition and Element Design
The 8000 series alloys are based on high-purity aluminum (≥98.3%) and enhanced with iron (0.6–1.0%) and silicon (0.4–0.8%) as core alloying elements, diverging from traditional alloying elements like copper (Cu) or magnesium (Mg). This strategic composition balances conductivity, strength, and workability, positioning them as cost-effective, lightweight alternatives to copper. Below is a comparative analysis of the 8000 series against other aluminum alloy families (1xxx–7xxx):
Series | Core Alloying Elements (wt%) | Typical Grades | Aluminum Purity (%) | Unique Design Goals |
1xxx | Pure Al(Al≥99.0%) | 1050, 1100 | 99.0–99.7 | High conductivity, corrosion resistance (chemical tanks, foil) |
2xxx | Copper (Cu: 3.8–4.9%) | 2024, 2017 | 90.0–94.0 | Ultra-high strength for aerospace (sacrifices corrosion resistance) |
3xxx | Manganese (Mn: 1.0–1.5%) | 3003, 3004 | 95.0–98.0 | Corrosion resistance, formability (cookware, cladding) |
4xxx | Silicon (Si: 4.5–6.0%) | 4032, 4043 | 85.0–90.0 | Low melting point, wear resistance (solder, pistons) |
5xxx | Magnesium (Mg: 2.2–6.2%) | 5052, 5083 | 92.0–95.0 | Marine-grade corrosion resistance (ships, automotive) |
6xxx | Magnesium + Silicon (Mg: 0.8–1.2%, Si: 0.4–0.8%) | 6061, 6063 | 95.0–97.5 | Balanced strength and extrudability (structural profiles) |
7xxx | Zinc (Zn: 5.1–6.1%) + Magnesium (Mg: 2.1–2.9%) | 7075, 7050 | 87.0–90.0 | Extreme strength for aerospace/military applications |
8xxx | Iron (Fe: 0.6–1.0%) + Silicon (Si: 0.4–0.8%) | 8011, 8030 | 98.3–99.0 | Lightweight copper replacement, balancing conductivity (≥60% IACS) and strength (120–170 MPa) |
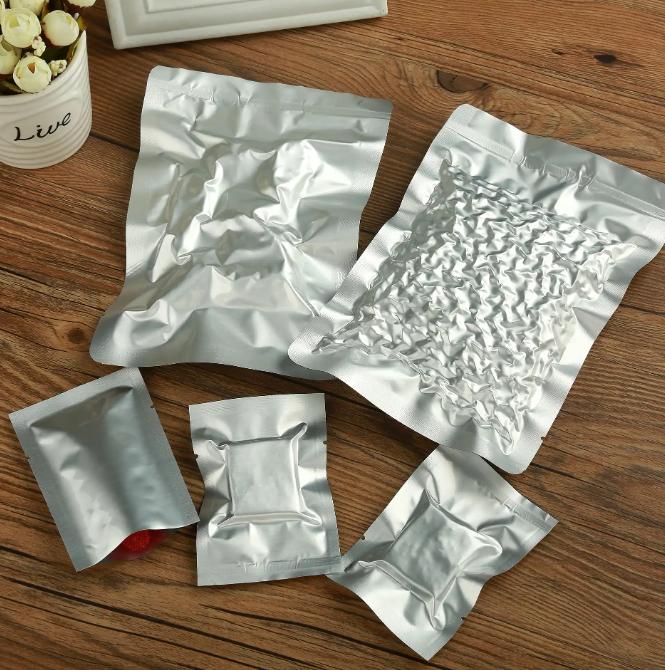
Common Forms of 8000 Series Aluminum
Form | Typical Grades | Applications |
Aluminum Foil | 8011 | Food packaging, capacitors |
Aluminum Wire | 8030 | Power cables, conductors |
Aluminum Sheet | 8079 | Battery current collectors, architectural cladding |
By precisely controlling Fe/Si ratios, 8000 series alloys achieve high electrical conductivity (≥60% IACS) while boosting tensile strength to 120–150 MPa (O-temper), addressing the weakness of pure aluminum (low strength and creep susceptibility). This compositional innovation makes them indispensable in packaging, energy transmission, and electronics.

Physical and Mechanical Performance Advantages
The strategic addition of lithium to aluminum in the 8000 series results in a distinctive set of physical and mechanical performance advantages that set it apart from other aluminum alloys.
The most notable of these is a significant reduction in density. Lithium, being considerably lighter than aluminum (with a density of approximately 0.53 g/cm³ compared to aluminum’s 2.7 g/cm³), directly contributes to lighter components. Studies on Al-Li alloys like 8090 have shown density reductions of around 8-10% compared to conventional aerospace alloys like 2024 or 7075. This weight saving is critical in industries like aerospace and automotive, where every kilogram shaved off translates to improved fuel efficiency, payload capacity, and performance.
Beyond density, 8000 series alloys often exhibit a higher specific stiffness (stiffness-to-weight ratio). The addition of lithium increases the Young’s modulus (a measure of stiffness) of aluminum without a proportional increase in density. For instance, 8090 can show an increase in Young’s modulus of around 10-15% compared to traditional aerospace alloys. This enhanced stiffness allows for the design of lighter structures with comparable rigidity, preventing excessive deformation under load.
Furthermore, certain 8000 series alloys demonstrate excellent fatigue crack growth resistance. This is particularly important in applications subjected to cyclic loading, such as aircraft structures. The unique microstructure resulting from lithium additions and optimized processing can hinder the initiation and propagation of fatigue cracks, leading to longer service life and improved safety. While the strength of 8000 series alloys can vary depending on the specific composition and temper, some alloys achieve competitive strength levels compared to established high-strength aluminum alloys. For example, cold-rolled AA8011 (H24 temper) reaches 150 MPa tensile strength with ≥5% elongation, outperforming pure aluminum (70 MPa, 30% elongation). This shows their attractiveness for structural applications where both lightness and strength are paramount.
The other features of 8000 series aluminum like conductivity and corrosion resistance are also excellent.
Electrical Conductivity: AA8011 foil achieves ≥61% IACS, close to pure aluminum (65% IACS) and far superior to copper-rich 2xxx alloys (30–40% IACS). In power transmission, AA8030 wires (61% IACS) weigh only 30% of copper equivalents. For instance, U.S.-based Southwire replaced copper cables with AA8030, cutting costs by 40% and improving installation efficiency by 50%.
Corrosion Resistance: A dense oxide layer (50–100 Å) extends service life by 30% in humid environments compared to 5xxx alloys.
The 8000 series’trinity of lightweight, high strength, and high conductivity positions it as a cornerstone material for energy and transportation industries seeking cost and performance optimization.
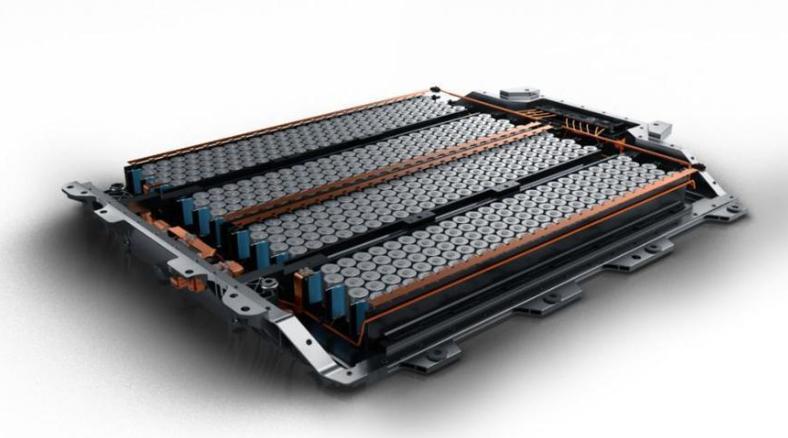
Differentiated Application Scenarios
The unique blend of properties offered by 8000 series aluminum alloys has led to their adoption and exploration in a range of specialized application scenarios, where their lightweighting and performance advantages are particularly valuable.
- Aerospace: This remains the most prominent and well-established application domain for 8000 series aluminum, particularly alloys containing lithium. The significant weight savings offered by Al-Li alloys like 8090 directly translate to reduced fuel consumption, increased payload capacity, and improved aircraft performance. As mentioned earlier, the Harrier GR5/7 was a notable early adopter, utilizing these alloys for fuselage skins and other structural elements. More recently, companies like SpaceX have reportedly used Al-Li alloys in structural components of their rockets to minimize weight. The increased stiffness also contributes to improved aerodynamic efficiency and structural integrity in aircraft and spacecraft.
- Packaging: While not as widespread as other aluminum alloys (like 1xxx or 3xxx) in traditional packaging like beverage cans, the unique properties of certain 8000 series alloys are being explored for specialized packaging applications. The potential for higher strength-to-weight ratios could lead to thinner-walled packaging with comparable structural integrity, reducing material usage and potentially transportation costs. Such as AA8079 foil (6–20 μm thickness) reduces oxygen permeability to ≤0.05 cm³/m²·day, extending pharmaceutical blister pack shelf life to 3+ years.
- EV Batteries: The burgeoning electric vehicle (EV) market presents a compelling new application space for lightweight materials. The battery pack is a significant contributor to the overall weight of an EV, impacting range and performance. 8000 series aluminum alloys, with their low density and potential for good structural integrity, are being investigated for use in battery enclosures and structural components within the battery pack. Reducing the weight of the battery system itself can directly contribute to increased range and efficiency. Such as AA8021 foil, rolled to 6 μm (industry benchmark), boosts lithium-ion battery energy density by 10%.
- Architecture: In the architecture and construction industries, aluminum alloys are valued for their corrosion resistance, recyclability, and aesthetic appeal. While 6xxx series alloys are widely used for structural elements, window frames, and facades, the unique properties of 8000 series aluminum could offer specific advantages in niche architectural applications. The higher stiffness could allow for the design of lighter yet structurally sound facade panels or roofing systems, potentially reducing the load on the supporting structure. Such as AA8011-H26 sheets (170 MPa strength) reduce skyscraper facade weight by 60% versus steel.
The adaptability of 8000 series aluminum to meet the diverse demands of industries underscores its importance in advancing technology and sustainability. Whether in aerospace or everyday packaging, its unique properties provide a versatile and reliable solution.
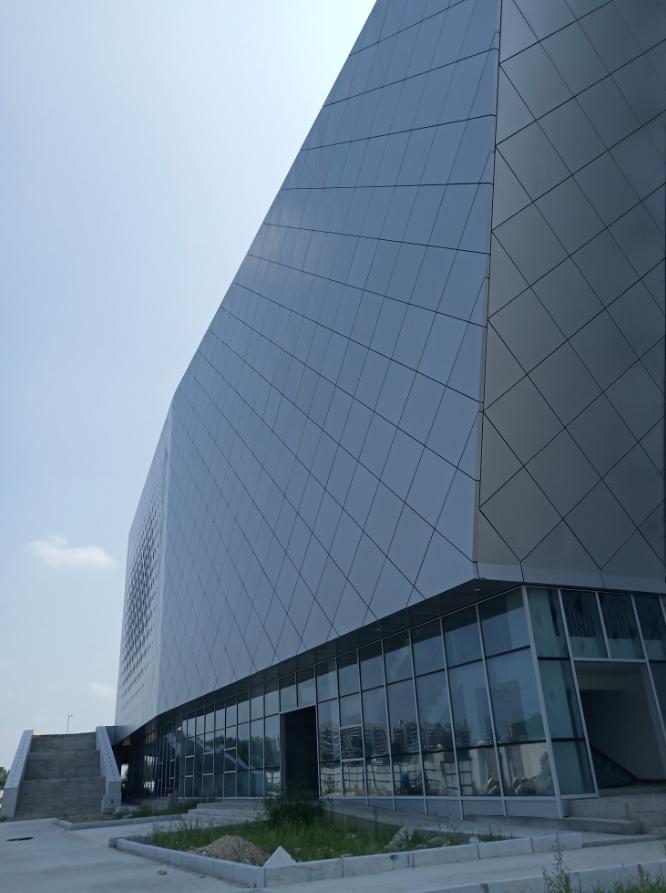
Process Technology Characteristics
Key innovations in 8000 series aluminum manufacturing include:
- Precision Rolling: Multi-pass cold rolling achieves ±0.5 μm thickness tolerance (e.g., AA8079 foil).
- Annealing: Segmented annealing (250–350°C) refines AA8011 grain size to ≤10 μm, enhancing elongation to 30%.
- Surface Treatment: Anodized hardness reaches 200 HV, 50% higher than 3xxx alloys.
Case Study: Battery Foil
CATL (Contemporary Amperex Technology) uses AA8021 foil processed via asynchronous rolling + corona treatment, achieving surface roughness (Ra) ≤0.2 μm. This improves electrode adhesion by 20%, enabling batteries with 4,000+ charge cycles.
Advanced processes push the boundaries of ultra-thin, high-strength aluminum, securing the 8000 series’ leadership in cutting-edge applications.
Market Competitiveness
The 8000 series aluminum dominates through cost-performance superiority, here is a comparison among common materials:
Metric | 8000 Series (AA8011) | Copper | 5xxx Series (AA5083) |
Price (USD/ton) | 3,200 | 9,500 | 4,800 |
Recycling Rate (%) | 95 | 80 | 85 |
Global Market Share (2024) | 38% | 22% | 15% |
However, the market competitiveness of 8000 series aluminum alloys is multifaceted and depends heavily on the specific application and the availability of alternative materials. Some market trends shows:
- Growing demand in sustainable packaging, driven by consumer and regulatory pressures.
- Increasing adoption in EVs and renewable energy systems.
- Competitive pricing compared to alternative materials like steel and composites.
A recent market analysis shows that the demand for 8000 series aluminum is projected to grow at a CAGR of 6% over the next decade. Its cost-effectiveness, environmental benefits, and technical superiority ensure that the 8000 series aluminum remains a competitive choice in various industries.
The 8000 series aluminum exemplifies innovation in material science, combining strength, versatility, and sustainability. Its unique alloy composition, exceptional performance characteristics, and adaptability across applications make it a vital material for modern industries. As manufacturing technologies evolve and global markets shift toward eco-friendly solutions, the prominence of 8000 series aluminum is poised to grow, shaping the future of materials engineering.
Related Products