Before You Buy: The 7 Key Characteristics of Choosing Aircraft Aluminum Sheets
Aluminum sheets are critical materials in aerospace manufacturing, accounting for 60%–80% of modern aircraft structures, from skin panels to load-bearing frames. As aircraft evolve toward lightweight and extended service life, the selection criteria for aircraft aluminum sheets have become increasingly stringent. This article systematically analyzes the 7 core performance parameters for aerospace-grade aluminum sheets, supported by technical specifications and real-world case studies.
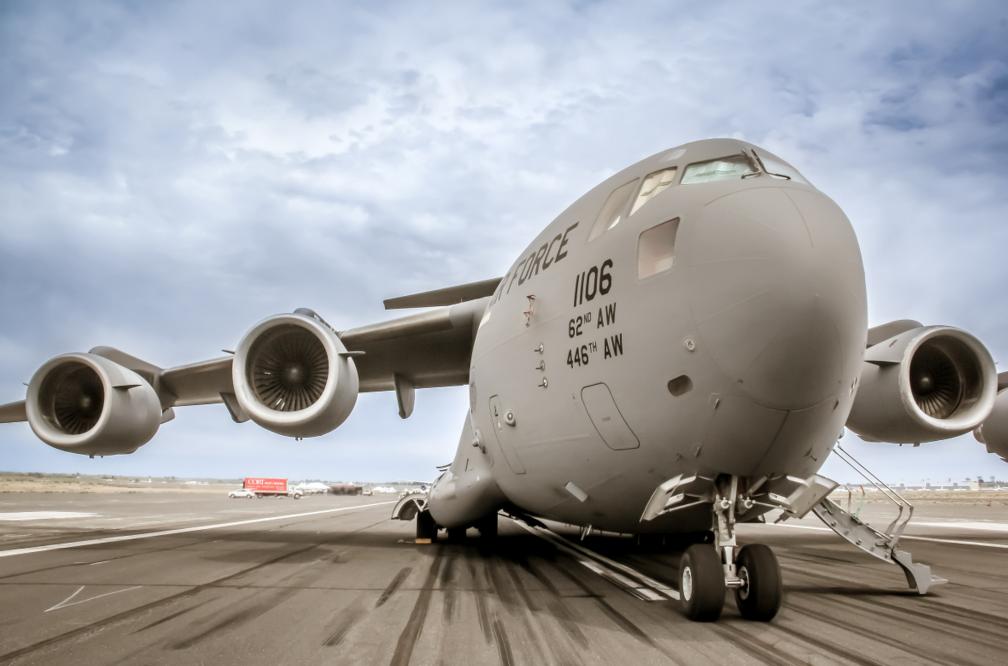
Characteristics 1: Mechanical Strength
Mechanical strength determines a material’s ability to withstand static and dynamic loads, including tensile strength, yield strength, and elongation. Here we take commonly used aluminum alloys as an example:
Alloy | Tensile Strength (MPa) | Yield Strength (MPa) | Elongation (%) | Application Example |
7075-T6 | 570 | 505 | 10 | Boeing 737 landing gear beams |
7050-T7452 | 540 | 490 | 11 | Airbus A380 wing panels |
2524-T3 | 450 | 360 | 12 | Boeing 777 fuselage skin |
High-strength aircraft aluminum alloys like 7050 achieve enhanced performance through Zn/Mg/Cu precipitation hardening, but elongation must be balanced to avoid brittle failure.
Characteristics 2: Fracture and Fatigue Properties
Aircraft components exposed to cyclic stresses must have fatigue resistance and fracture toughness.
Critical Data
- Crack Growth Rate (Griffith’s Law): For 7050 alloy for C919 wing spars, up to a value of 1.5×10⁶ mm/cycle at ΔK=20 MPa√m can be achieved.
- KIC: 7150 alloy used in Boeing 747-8 cargo doors measures KIC=35 MPa√m, proving a very significant improvement over previous materials by more than 40%.
- Fatigue Limit: Tempered 2024-T42 alloy scale for A350 window frame structures showed endurance limit of sustaining stress of 180 MPa for at least ten million cycles.
Derived primarily from secondary sources, Al-Li alloy 2099 in the Boeing 787 was reported to not only increase the fatigue life by three times but also to lower weight by fifteen percent on fuselage stringers.
Suppression of crack initiation relies on microstructured optimized alloys that are engineered with damage-tolerant properties.
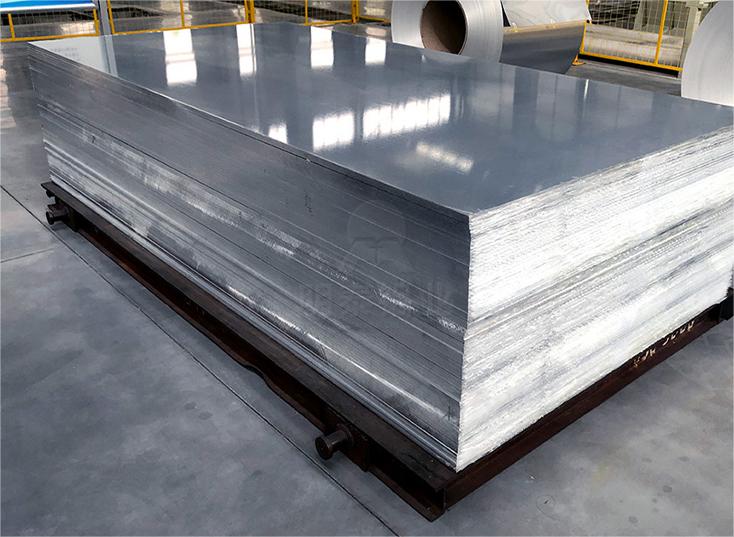
Characteristics 3: Environmental Resistance
Aircraft aluminum sheets need to resist corrosion from complex environments such as salt spray, humidity, and extreme temperatures.
Testing Standards & Performance
Environment | Test Standard | Requirement | Alloy Solution |
Marine Atmosphere | ASTM G85-A3 | 3,000h salt spray resistance | 5052-H32 (0.02 mm/yr) |
Stress Corrosion | ASTM G47 | SCC threshold ≥300 MPa | 7B50-T7751 (350 MPa) |
Cryogenic (-253°C) | MIL-HDBK-5H | 90% strength retention | 2219-T87 (480 MPa) |
For example, the Long March 5 rocket fuel tanks use 2219-T87 aircraft aluminum sheets, retaining 300 MPa strength in liquid oxygen (-183°C).
Alloying elements like Cr and Sc improve environmental resistance in aircraft aluminum sheets but require cost-process trade-offs.
Characteristics 4: Process Compatibility
The forming, welding and heat treatment processes of aircraft aluminum sheets directly affect manufacturing efficiency and finished product quality.
Comparison of Common Process Performance
Process | Key Parameter | 6061-T6 | 7075-T6 |
Formability | Anisotropy coefficient | 0.8 | 0.6 |
Weldability | Welding efficiency | 0.85 (TIG) | 0.6 (FSW) |
Heat Treatment | Quench depth | 50 mm | 150 mm |
For example, the Airbus A320 uses laser-MIG hybrid welding technology, which improves the welding efficiency of 7075 alloy by 40% and reduces the heat-affected zone to 2mm.
High-strength aluminum alloys (such as 7050) need to be matched with advanced processes (such as stir friction welding) to avoid traditional welding defects.
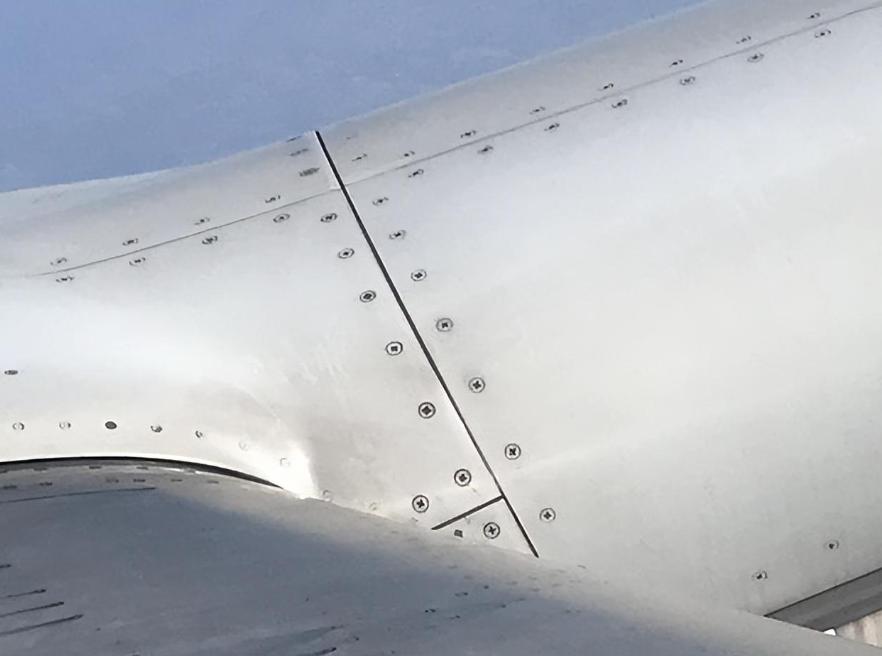
Characteristics 5: Special Functional Requirements
In certain scenarios, aluminum sheets need to have additional functions such as electromagnetic shielding, impact resistance or thermal conductivity.
Functional Solutions
Requirement | Implementation | Application Example |
EMI Shielding | 1060 alloy (80dB @1GHz) | Radar compartment shielding |
Impact Resistance | 5083-H116 (380 MPa dynamic) | Helicopter armor plates |
Thermal Conductivity | 6063-T5 (218 W/m·K) | Avionics heat sinks |
Functionalized aluminum sheets can be adapted to multiple scenarios through composition design (such as high-purity aluminum) or composite treatment (such as Al-SiC coating).
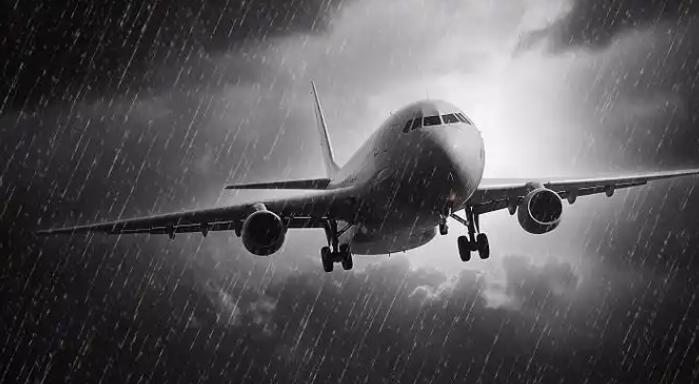
Characteristics 6: Microstructural Control
Aircraft aluminum sheets necessitate intricate regulation of grain size, precipitates, and texture since microstructure dictates macroscopic properties.
Optimization Techniques including:
- Grain Refinement: Increases KIC by 25% when the 7050 alloy is aged with multi-stage aging due to a reduction in grain size from 100μm to 20μm.
- Precipitate Engineering: Limits η’ phase to ≤10nm during retrogression and re-aging (RRA) of 7075 alloys.
- Texture Control: Decrease anisotropy in 2024-T3 alloy from 1.2 to 0.9 through cross rolling.
As an example, dual-stage solution treatment on China’s 7A85 aircraft aluminum sheets results in over 95% of coarse secondary phases being removed.
For further investigation into the microstructural optimization of aircraft aluminum sheets, advanced characterization techniques such as EBSD and TEM are essential.
Characteristics 7: Testing and Certification
Aircraft aluminum sheets must comply with rigorous testing and global certification standards.
Testing Protocols including:
Test Type | Standard | Acceptance Criteria | Application Scope |
Nondestructive | ASTM E2375 (UT) | Detect ≥Φ1.2mm flaws | Wing spar inspection |
Mechanical | ASTM E8/E21 | Strength tolerance ≤5% | Material qualification |
Airworthiness | Boeing BMS7-347 | Full compliance with AMS4050L | Commercial aircraft |
For example, C919 aircraft aluminum sheets require COMAC CTSO-C153 certification, involving 16 performance tests and 3-year service simulation.
Global supply chains necessitate alignment of aircraft aluminum sheets with FAA, EASA, and CAAC standards.
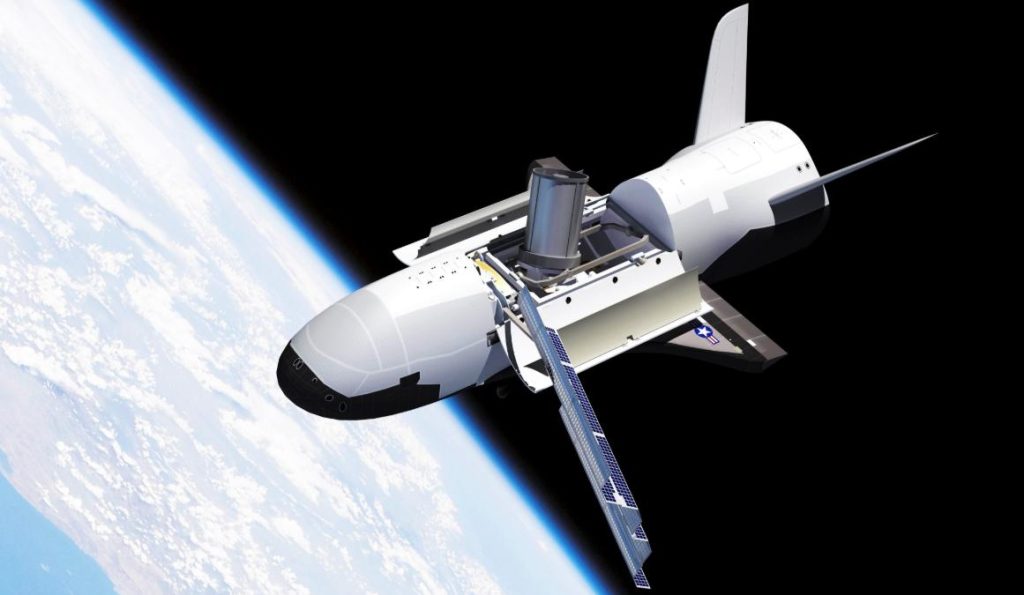
How to Make a Decision?
Selecting aircraft aluminum sheets requires prioritizing parameters based on application scenarios, for example:
- Commercial Aircraft: Fatigue life (e.g., 2524-T3), weight savings, and cost efficiency.
- Military Aircraft: Ultrahigh strength (e.g., 7055-T7751) and impact resistance.
- Spacecraft: Cryogenic performance (e.g., 2195-T8) and weldability.
Scenario-Based Selection Guide:
Application | Priority Parameters | Recommended Alloys |
Airliner Fuselage | Fatigue resistance, damage tolerance | 2524-T3, 2324-T39 |
Fighter Wings | Tensile strength, impact resistance | 7055-T7751, 7085-T74 |
Rocket Tanks | Cryogenic toughness, weldability | 2195-T8, 2219-T87 |
Choosing the right aircraft aluminum sheet entails balancing all seven performance parameters. Prioritization depends on the application such as a commercial airliner, military aircraft or other aerospace structures. These characteristics, when aligned with operational needs, result in optimal performance, safety and cost-effectiveness in aircraft designs.
Looking for an aircraft aluminum sheet supplier? Don’t hesitate to get in touch with Lanren Aluminum.
Related Products